Verified Suppliers|Full Compliance with EU Standards|24H Technical Support
Why choose a fully automatic horizontal hydraulic baler?
Experience seamless, hands-free baling with our fully automatic horizontal baler. Perfect for high-volume operations.
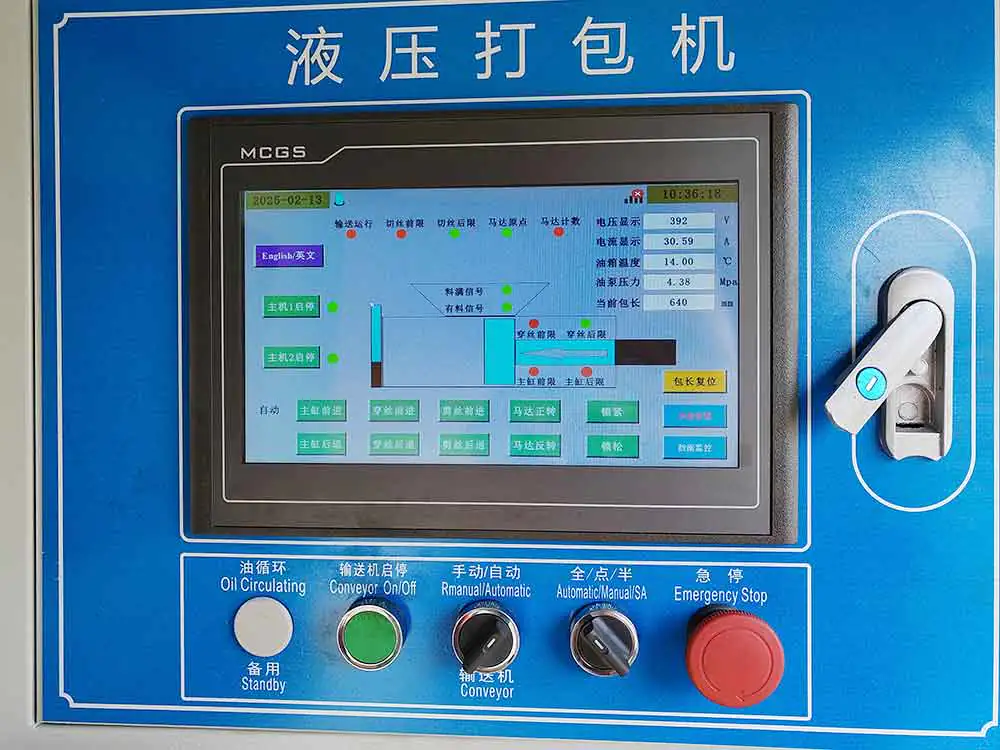

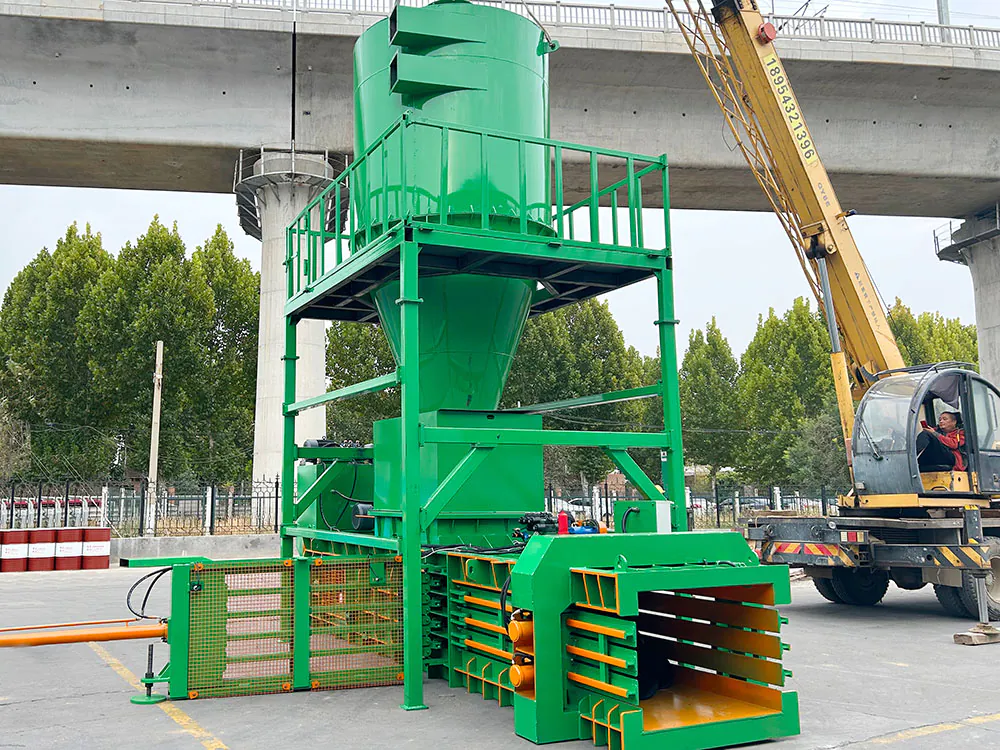


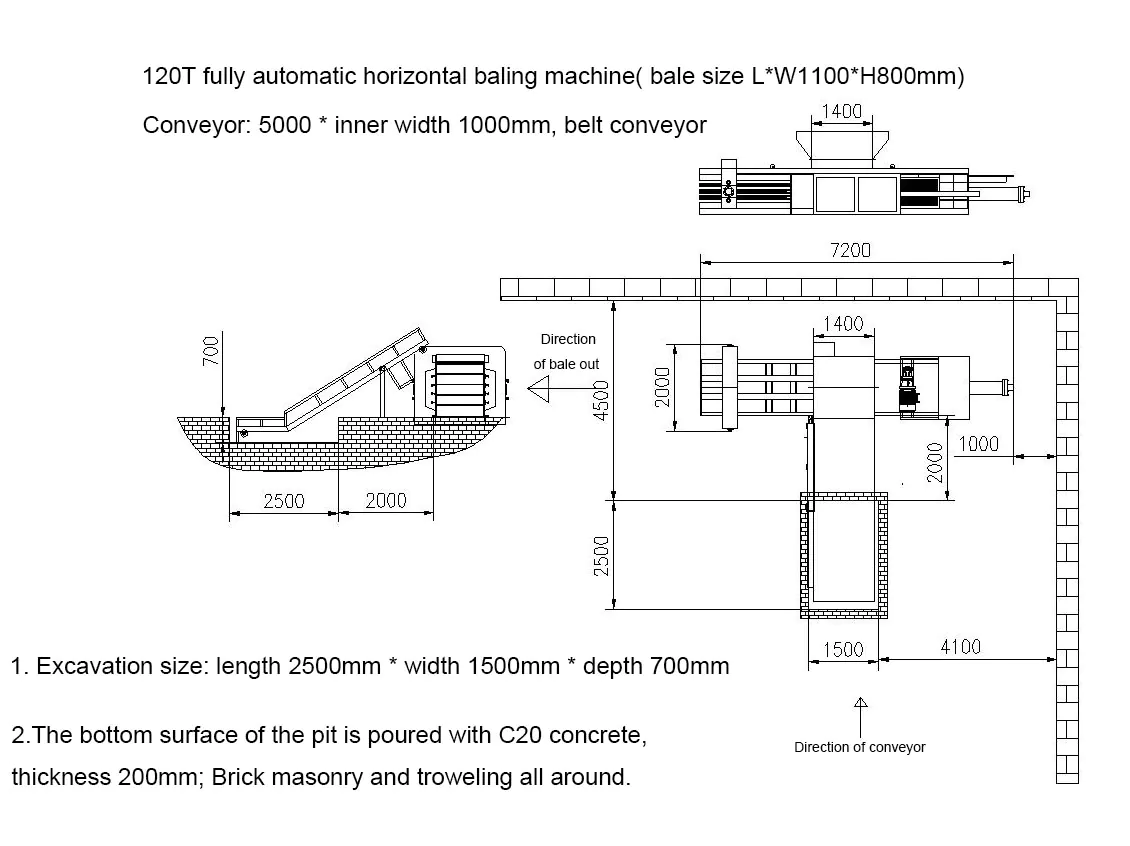
How about a traditional manual baler?
Requires a lot of labor
Uneven packing density
Low production efficiency
What can the fully automatic baling machine solve?
PLC fully automatic operation, reducing labor
High pressure compression, uniform density
Continuous feeding, uninterrupted packaging
How to choose the right horizontal baler for you?
“Safe design | Suitable for cartons, plastics, | Easy to operate”
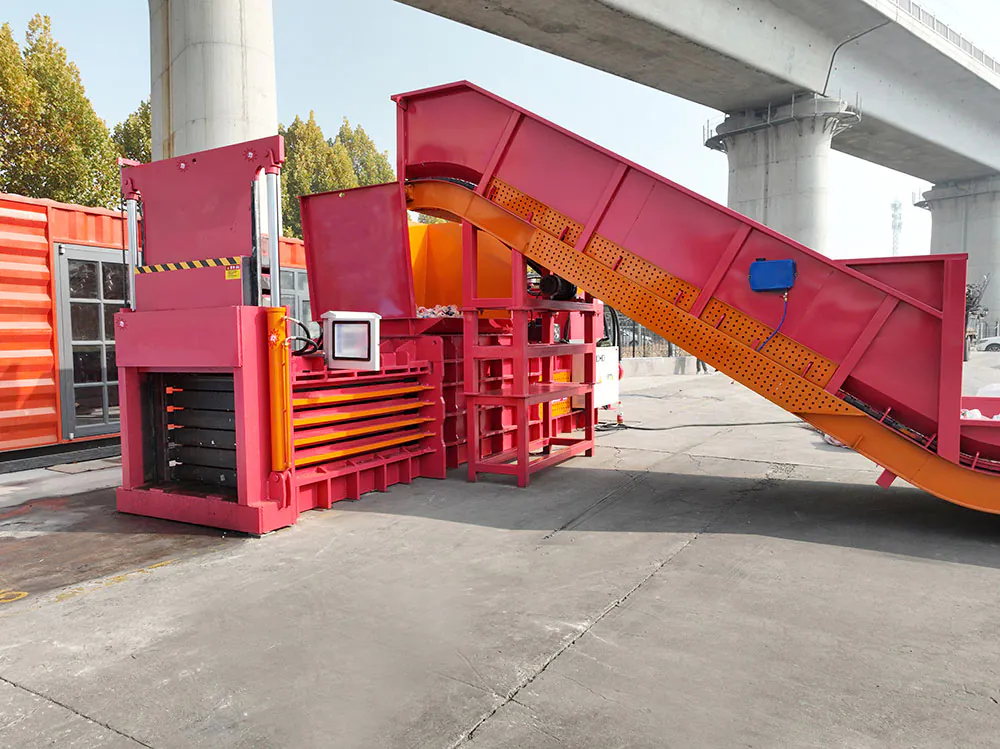
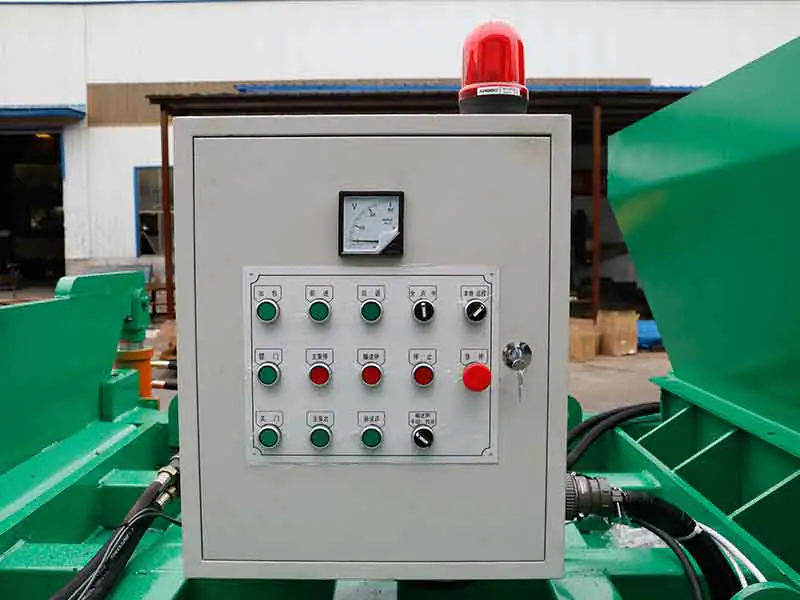

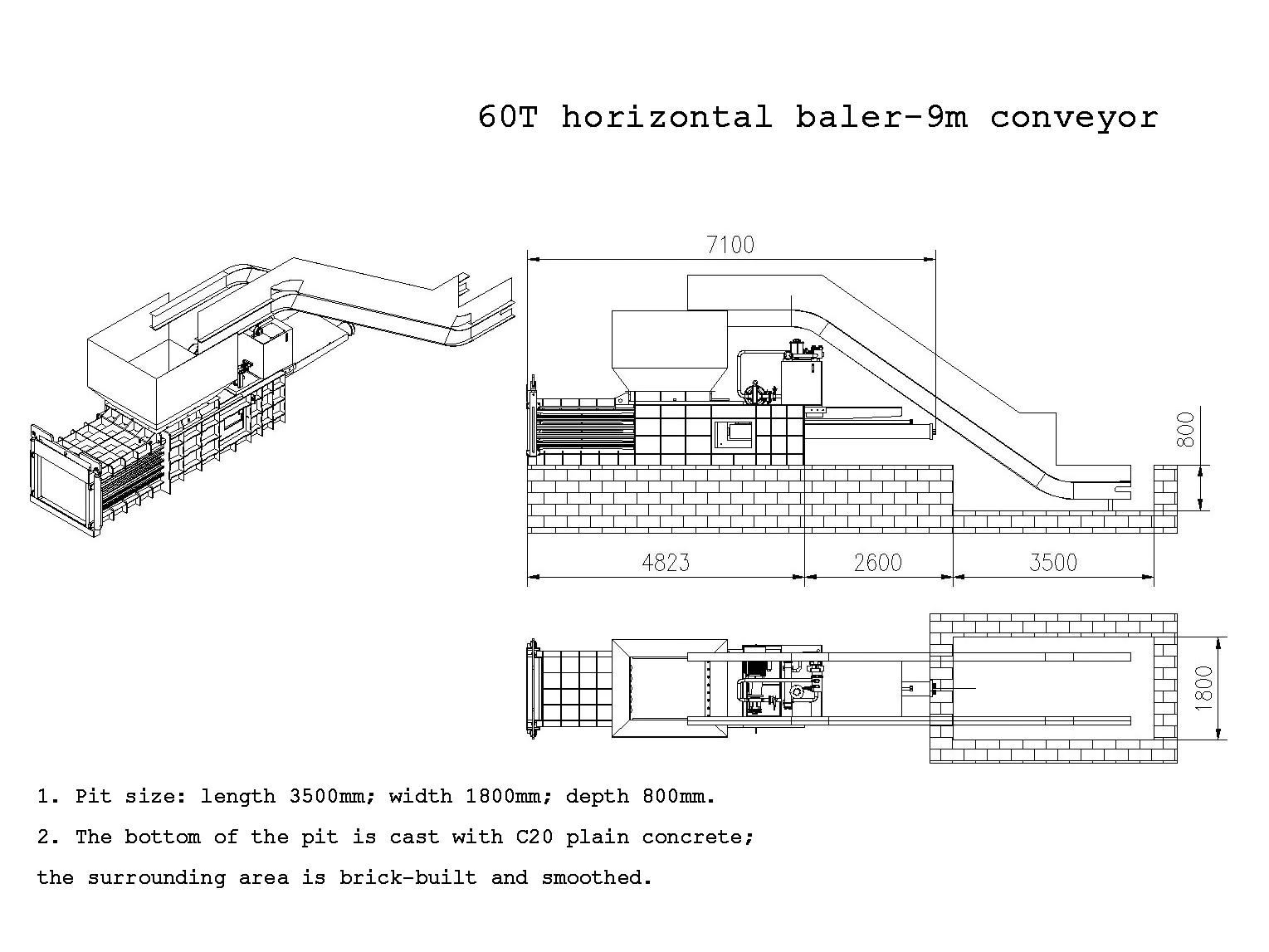
Pressure: Customer Cases 120T (Customization available, up to 300T+)
Degree of automation: Automatic packing , Manual rope threading , Manual rope binding
Baler size: L1700*W1100*H850 mm
Bale weight: 300-400 kg for PET bottles , 500-600kg for cardboard
Inlet: 1400*1100 mm
Main cylinder: 230 mm*2800 mm
Outlet method: Cylinder push bag
Working efficiency: 4-6 pieces/h
Operating system (Mitsubishi/Xinjie): Control box
Motor: 22 KW
Voltage: 380V/50 HZ/ 3phase/ 900 RPM
Install a lift door baler, increasing efficiency by 30% !
Saves 50% labor cost than traditional baler !
Is a Vertical Baler Right for Your Business?
Ideal for small to medium-sized businesses looking for an efficient and space-saving baling solution. Affordable, user-friendly, and perfect for low to medium-volume operations.

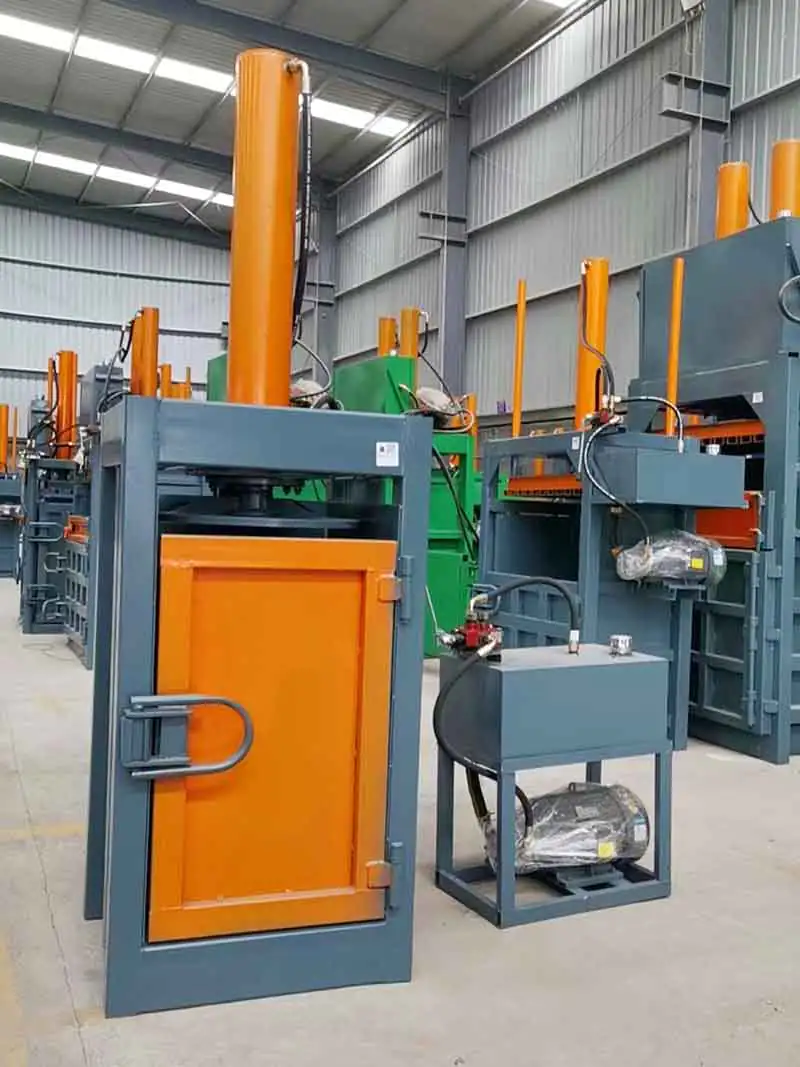
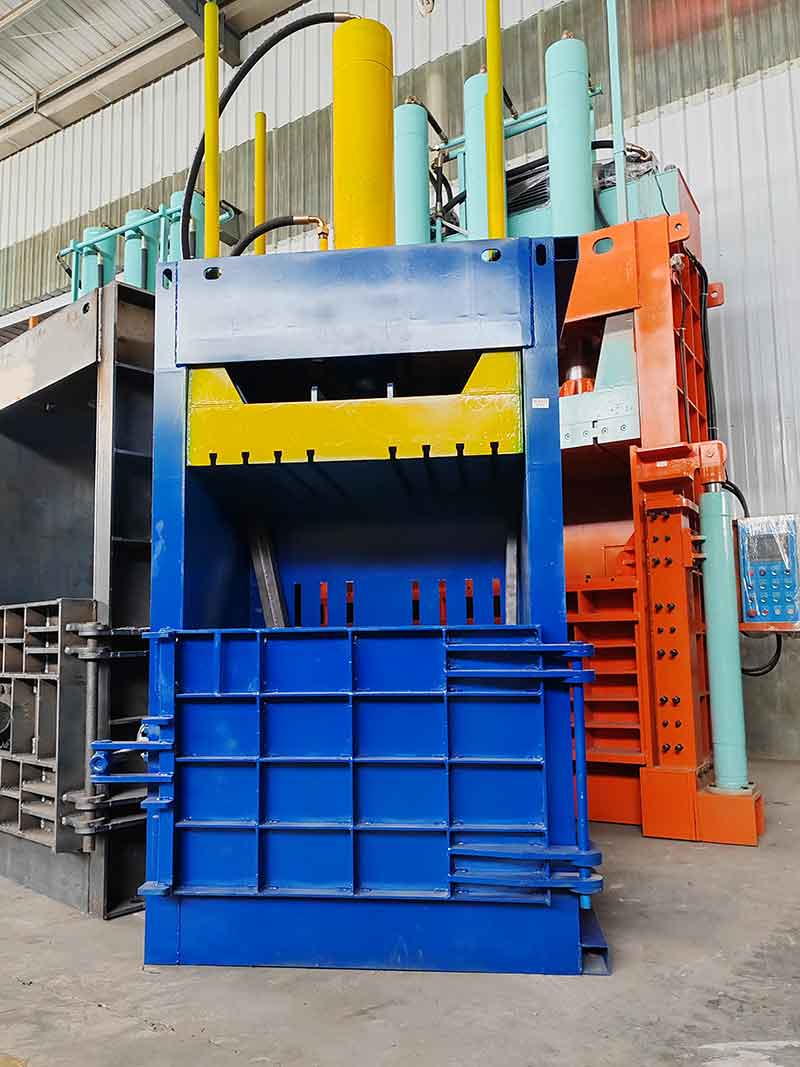
Compact Design
Fits easily into smaller facilities with limited space.
Easy Operation
Simple controls make it accessible for all skill levels .
Low Initial Cost
An affordable entry point into baling technology
Versatile Applications
Handle paper, cardboard, plastic, and more with ease.
—— “Don’t make the same mistakes I made!”
✈️ Q1: I heard that Chinese machines are cheap, but are the quality and certification reliable? Our customs checks CE very strictly!
Alas, I was also entangled with this issue three years ago! At that time, a Zhejiang factory I cooperated with patted its chest and said that it had a CE certificate. As a result, when the goods arrived in Poland, the customs required the “Declaration of Conformity for Machinery Directive 2006/42/EC”. The factory could not produce it directly and it was almost returned!
Practical advice: Don’t just look at the certificate number! Ask the manufacturer to send you directly:
✅ EC Type Examination Cert for the whole machine (with the seal of the EU Notified Body)
✅ IP protection level test report of the hydraulic cylinder (especially for machines that handle metal waste)
🔧 Q2: How to solve the voltage adaptation problem? The voltage here is different from that in China!
I have a customer in Mexico. The factory sent him a standard 380V/50Hz machine, but the local voltage is 220V/60Hz! He spent 7,000 US dollars to change the line…
Require the factory to do the following:
▷ Provide a real shot of the coil/motor nameplate (to see if it is marked with “50/60Hz compatible”)
▷ In the test video, plug in the inverter to demonstrate the operation at different voltages
📦 Q3: Will it rust into scrap metal when shipped by sea? How do you pack it?
Ha, the two machines I ordered before were wrapped in ordinary plastic film by the manufacturer. As a result, when they arrived in Indonesia, the hydraulic valves were all rusty! Later I learned that VCI anti-rust film + desiccant must be used for sea transportation.
Tricks to avoid:
“Please attach a video of the packaging process. I need to see three things:
① Spray anti-rust oil on metal parts
② The circuit board is sealed with a vacuum bag separately
③ The humidity of the wooden box is less than 10% (put a hygrometer inside the box)”
💰 Q4: In addition to the price of the machine, are there any other hidden costs to pay attention to?
Lesson learned from blood: A German customer bought a machine and found out that —
▷ The blade needs to be sharpened every week, and there is no suitable grinder locally (spending an extra $200 per month on outsourcing)
▷ The oil seal model is special, and the price quoted by the European supplier is 5 times the price in China!
Smart approach:
Ask the factory to provide the “Guide to Replacement of Consumable Parts” to confirm:
✔ General models can be purchased locally (such as SKF bearings)
✔ Attached is a Chinese-English comparison table of 10 common fault codes
🤖 Q5: How to guarantee after-sales service? You can’t fly to China as soon as there is a problem, right?
Having experienced the 48-hour jet lag video repair of the machine, I strongly request:
❶ The contract should clearly state “must have a remote diagnostic port” (it is best to be able to check the pressure value on a mobile phone APP)
❷ Confirm in advance that they have spare parts in the warehouse next to your country (for example, if they sell to Chile, ask if there is a cooperation point in Peru)
⚠️ Be wary of rhetoric: “We have global after-sales” → It may actually be just a translation company phone number!
💡 Q6: I want to see the real level of the factory, but what should I do if I can’t come to China for factory inspection after the epidemic?
Teach you a trick-
▶️ Let the sales manager use Douyin to live broadcast the workshop (dynamics are more real than posed videos)
▶️ Request to provide the bill of lading number of recent exports to countries in the same region as you (check the authenticity of the ship information network)
▶️ Key workers show their faces in self-introduction videos (“I am Li Gong, responsible for circuit testing for 10 years!”)
The last piece of advice🔔:
Be wary of those salesmen who are eager to ask “How many units do you want? There is a discount if you order now!” A truly high-quality factory will ask you in return:
“What waste does your company mainly handle? What is the average moisture content? We need to adjust the pressure parameters.”
Remember – the more details you pay attention to, the more reliable the cooperation will be.
(Bosses who need the “List of Necessary Documents for Import Customs Clearance”, please contact us to send it to you!)